Discover What is Porosity in Welding and Its Effect on Structural Honesty
Discover What is Porosity in Welding and Its Effect on Structural Honesty
Blog Article
The Scientific Research Behind Porosity: A Comprehensive Guide for Welders and Fabricators
Understanding the elaborate mechanisms behind porosity in welding is essential for welders and producers making every effort for impeccable craftsmanship. From the structure of the base products to the complexities of the welding process itself, a multitude of variables conspire to either worsen or relieve the existence of porosity.
Comprehending Porosity in Welding
FIRST SENTENCE:
Evaluation of porosity in welding reveals essential insights into the honesty and high quality of the weld joint. Porosity, characterized by the existence of dental caries or spaces within the weld steel, is a common worry in welding processes. These voids, if not correctly addressed, can endanger the structural honesty and mechanical properties of the weld, leading to prospective failures in the completed item.
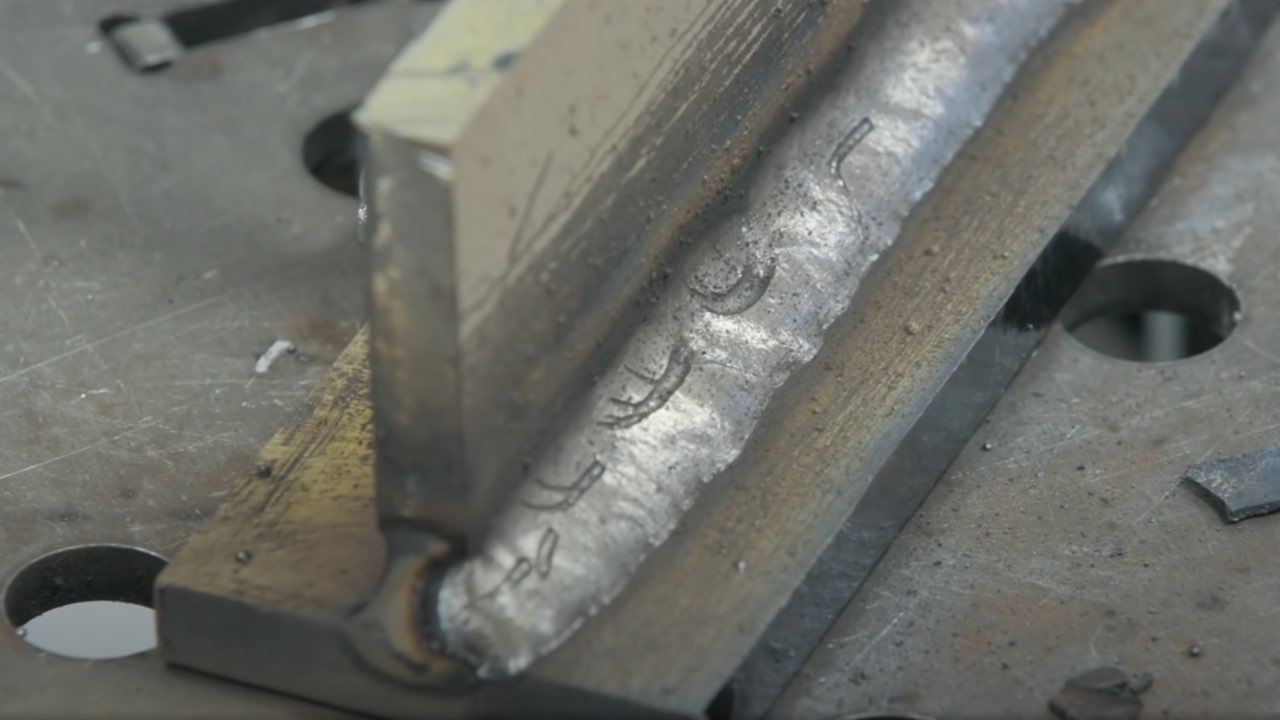
To identify and measure porosity, non-destructive screening methods such as ultrasonic testing or X-ray assessment are commonly utilized. These techniques permit the recognition of interior issues without jeopardizing the integrity of the weld. By examining the size, shape, and distribution of porosity within a weld, welders can make informed decisions to boost their welding procedures and achieve sounder weld joints.
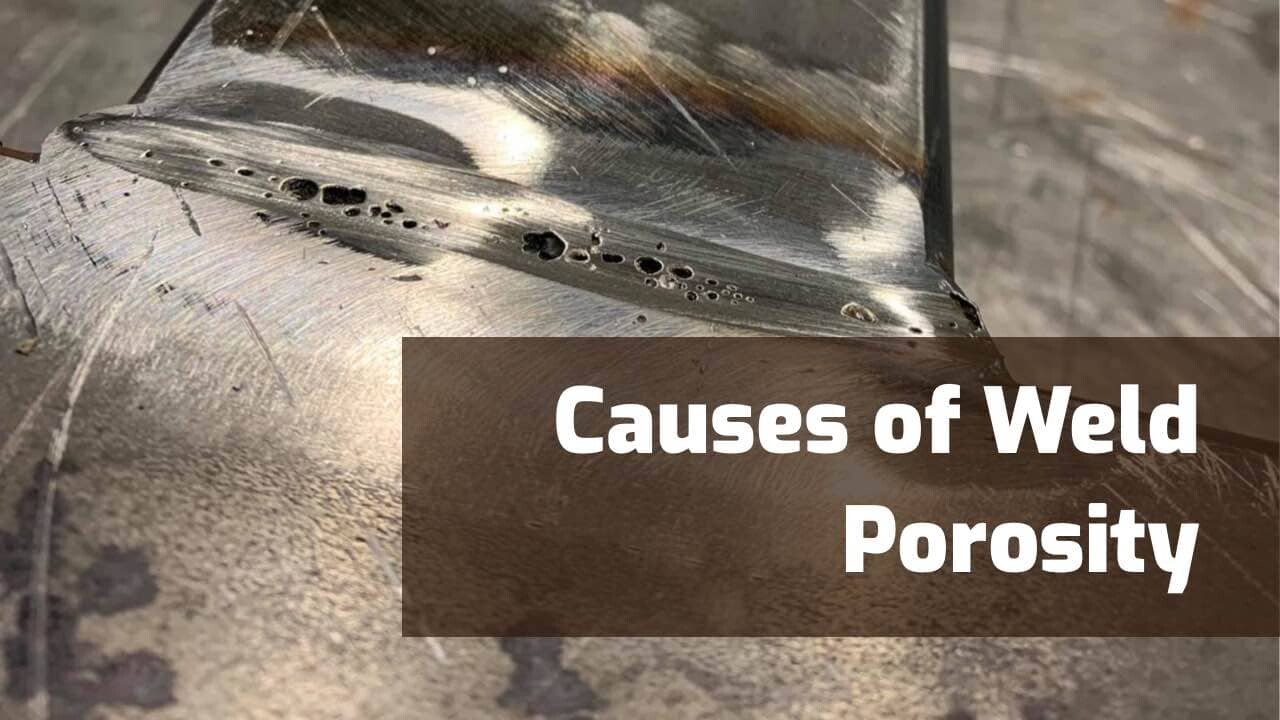
Aspects Affecting Porosity Development
The event of porosity in welding is influenced by a myriad of variables, varying from gas securing effectiveness to the details of welding parameter setups. Welding criteria, consisting of voltage, current, travel speed, and electrode type, likewise effect porosity formation. The welding strategy employed, such as gas metal arc welding (GMAW) or secured steel arc welding (SMAW), can affect porosity development due to variations in heat distribution and gas protection - What is Porosity.
Results of Porosity on Weld High Quality
The presence of porosity additionally deteriorates the weld's resistance to deterioration, as the entraped air or gases within the gaps can respond with the surrounding environment, leading to deterioration over time. Additionally, porosity can impede the weld's capacity our website to withstand stress or effect, further threatening the general high quality and reliability of the bonded structure. In crucial applications such as aerospace, automotive, or architectural constructions, where safety and security and longevity are paramount, the damaging results of porosity on weld high quality can have extreme repercussions, stressing the significance of reducing porosity via appropriate welding strategies and procedures.
Methods to Minimize Porosity
Additionally, making use of the suitable welding specifications, such as the proper voltage, current, and travel speed, is important in avoiding porosity. Maintaining a regular arc size and angle throughout welding likewise aids reduce the possibility of porosity.

Utilizing the appropriate welding method, such as back-stepping or using a weaving activity, can also aid distribute warmth evenly and minimize the opportunities of porosity development. By carrying out these methods, welders can effectively minimize porosity and produce premium welded joints.
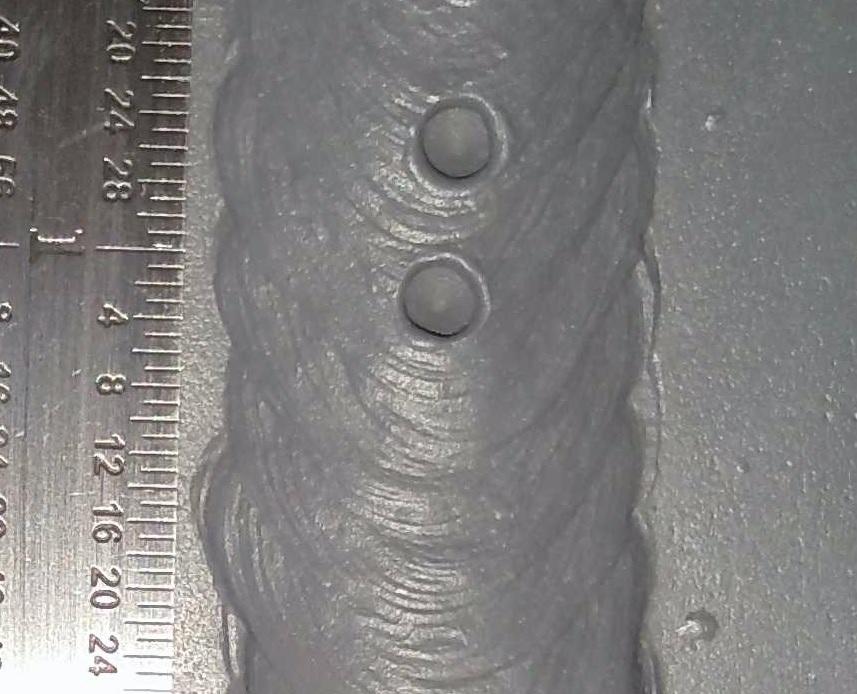
Advanced Solutions for Porosity Control
Implementing cutting-edge technologies and cutting-edge approaches plays a pivotal function in attaining premium control over porosity in welding procedures. One advanced solution is the use of advanced gas mixes. Shielding gases like helium or a combination of argon and hydrogen can help lower porosity by offering much better arc security and enhanced gas protection. Additionally, employing innovative welding techniques such as pulsed MIG welding or see this here customized environment welding can also assist mitigate porosity concerns.
One more innovative remedy entails using innovative welding tools. Utilizing tools with built-in attributes like waveform control and innovative power resources can improve weld quality and decrease porosity dangers. In addition, the application of automated welding systems with exact control over parameters can substantially reduce porosity flaws.
In addition, including advanced monitoring and evaluation innovations such as real-time X-ray imaging find more or automated ultrasonic testing can assist in spotting porosity early in the welding procedure, permitting immediate corrective actions. In general, incorporating these innovative services can substantially enhance porosity control and enhance the overall high quality of welded elements.
Verdict
To conclude, recognizing the science behind porosity in welding is necessary for welders and makers to generate top quality welds. By determining the aspects affecting porosity development and executing techniques to minimize it, welders can enhance the overall weld quality. Advanced solutions for porosity control can additionally boost the welding procedure and guarantee a solid and dependable weld. It is necessary for welders to constantly enlighten themselves on porosity and implement finest methods to accomplish optimum outcomes.
Report this page